Laboratory Safety in Biomedicum
Here you will find information on rules, regulations and guidance in different areas of laboratory safety.
Good Laboratory Practices
Good Laboratory Practices (GLPs) are to be followed in the laboratories at all times;
- Do not eat, drink, apply cosmetics, use tobacco products, or handle food in the lab.
- Wear personal protective equipment such as lab coats and gloves in the lab, but never in the office areas or common areas.
- Observe cleanliness and maintain good order in your work environment.
- Avoid spills, splashes and formation of aerosols when handling hazardous liquids or powders.
- Handle needles and sharps safely. Dispose of these in appropriate sharps containers.
- Manage waste safely and responsibly. Use correct bins and labeling.
- It is okay to make mistakes - if you are unsure on how to safely handle a situation, materials, or of the risk associated with any procedure, always seek guidance.
1. Risk assessments
All procedures involving a possible risk need to be risk assessed (AFS 2001:1).
Pregnant and nursing staff
2. Biosafety
Biosafety means the protection of people and environment from exposure to contagious biological material handled in the laboratory.
Issues or questions regarding biosafety should be addressed to the department's biosafety officers, or to the Biosafety coordinator at Karolinska Institutet, Carina Bengtsson. Contact FM Helpdesk for help with e.g. BSL2 signs for the facilities.
Biosafety at Karolinska Institutet
Biomedicum's Biosafety officers
Stefano Gastaldello
Senior Research SpecialistHåkan Karlsson
Principal ResearcherAkos Vegvari
Senior Research SpecialistAlexander Zulliger
Biomedical Scientist3. Chemical safety
Work with chemical substances is regulated by laws, rules and regulations – both from Sweden and the EU – covering work environment as well as external environment issues. The purpose of these regulations is to create a safe work environment, to protect the external environment, and to ensure a sustainable development.
Chemical safety at Karolinska Institutet
In Biomedicum the Facility Management (FM) team work preventive to minimize the risk of laboratory accidents. Issues and questions regarding chemical safety can be addressed to Biomedicum’s chemical representative.
Biomedicum's Chemical representative
Ingrid Delin
CoordinatorCMR chemicals
Carcinogenic, mutagenic, reprotoxic (CMR) chemicals must be handled in accordance with the Swedish Work Environment Agency's regulations. Among other things, an investigation into whether the substance can be replaced by a less dangerous one must be carried out before it is used, and the method must be risk assessed.
At Biomedicum, there are CMR rooms in some of the blocks. Log lists for these rooms can be found at the bottom of the page under "Documents"
3.1 KLARA chemical register
According to Swedish legislation (AFS 2011:19 and SFS 1998:901) all organizations and companies must keep a register of chemical products that may pose a risk to health and/or environment.
At Karolinska Institutet, this registry is conducted in KLARA and kept up to date by an annual inventory at the beginning of each year. All active research groups with chemical holding need to have a chemical inventory taker registered in KLARA.
In addition to a chemical register in KLARA, there are also modules for risk assessments involving chemicals, isotope register, and fire safety self-monitoring.
Use your KI credentials to log in to KLARA. Contact FM Helpdesk for access to your research group’s register of chemicals.
Biomedicum's KLARA administrators
Ingrid Delin
CoordinatorStefan Klinter
Team ManagerRisk assessments of chemicals
For methods involving chemicals the written assessment can be performed in KLARA. Contact your groups KLARA inventory taker for more information, or your KLARA administrator via FM Helpdesk. Read more on chemical risk assessments here.
The KLARA register can be used to find chemicals, also from other research groups, instead of purchase of new. Contact your KLARA administrator via FM Helpdesk to locate chemicals.
3.2 Chemical storage
All hazardous chemicals need to be stored in ventilated or fire safety cabinets, when not in use. Ventilated cabinets are available in most labs in the quarters and space is divided between the research groups locally. Flammable chemicals that need to be stored in cold must be stored in a cold-room or in spark-free fridge/freezer purchased by the research groups. The storage regulations also apply to chemical waste. Chemicals must also be stored with no risk of mixing with incompatible chemicals.
Contact FM Helpdesk if you have any questions on how to store and handle chemicals safe.
3.3 Gases
A number of regulations must be observed for internal transport, storage, and usage of gas in order to handle it safely.
Always contact FM laboratory safety coordinators via FM Helpdesk before purchasing and utilizing new types of gases in the laboratory.
Biomedicum house gases
Carbon dioxide (CO2), Nitrogen (N2) and Carbogen (CO2 + O2) are centrally provided in Biomedicum.
If other grades of these gases, or other gases, are required, this may be purchased as loose containers.
Gas safety training
Training and good knowledge of different types of gases and their risks are required for all handling. Students or temporary hired staff (consultants) may not handle gas cylinders.
Online training (in Swedish) and self-study training (in English and Swedish) is available via FM.
Risk assessments of gases
Before installation or usage, it is important to consider hazards and risks associated to the gas, what control measures are in place, if there is need for alarms, how to perform leakage test or checks, and emergency procedures. Template for risk assessment before installation is found here (Swedish), and the risk assessment for gas usage can be performed in KLARA.
Gas storage requirements in Biomedicum
General storage requirements
- All bottles should stand upright and be chained to a wall, bench, or gas trolley. This also applies to empty gas cylinders. Smaller gas cylinders don’t require a chain if they stand upright in a metal basket and are not in danger of falling.
- Gas cylinders must not be stored near heat sources or hot surfaces or stored in such a way that they risk mechanical impact.
- Gas cylinders may not be stored together with combustible materials such as cardboard boxes.
- Toxic gases should not be stored together with oxidizing or flammable gases. Flammable gases should not be stored together with oxidizing gases.
- Empty bottles and full bottles should be stored separately and be well labeled.
- Do not remove or damage the supplier-labels.
- All gas cisterns should be labelled with the name and telephone number to a contact person.
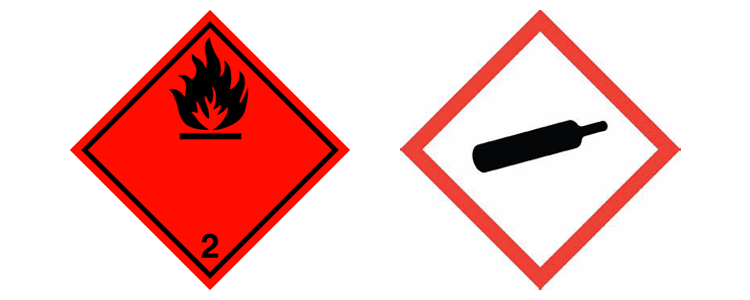
Flammable gas
(e.g. Methane, Ethane, Acetylene, Hydrogen, Ammoniac)
Flammable gases should be stored inside the specific gas storage rooms in each block, and according to KI's rules for storing KI's rules for storing flammable goods.
Flammable gas should not be stored together with oxidizing, corrosive or toxic gases.
Exception: Small amounts of flammable gas (Camping gas bottles, approx. 200ml) may be stored inside the fire safety cabinets together with flammable liquids in general laboratories.

Note that premises, or part of premises, where open handling of flammable goods may cause an explosive atmosphere, requires EX classification and an area classification plan. To avoid explosive environments to arise it is preferable to handle flammable goods in closed systems or in ventilated areas (fume hood, benches etc). For more information, see KI's rules for flammable goods.
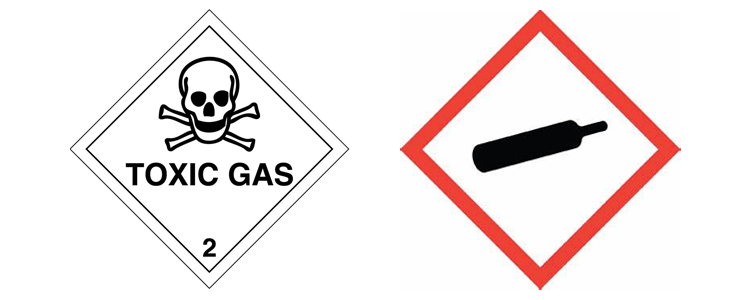
Toxic gas
(e.g. Hydrogen sulphide, Anhydrous ammonia, Carbon monoxide)
Toxic gases must be stored inside the specific gas storage rooms located in each block, in well-ventilated cabinets. Toxic gases may temporarily be present in the general laboratories during use.
Toxic gas may not be stored together with flammable gas.
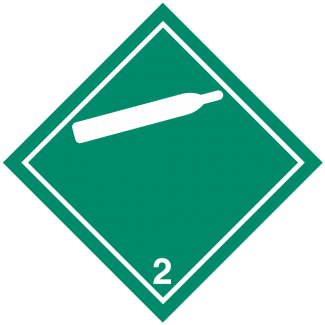
Inert gas
(e.g. Nitrogen, Helium, Argon, Carbon dioxide)
Inert gases can be stored in the quarters, but the size limit of the cisterns in the open laboratories is 20L. Between experiments, the cisterns should be stored in the gas storage room.
When writing the risk assessment and working with inert gases, consider the risk that inert gases may dilute or displace the oxygen normally present in the atmosphere.
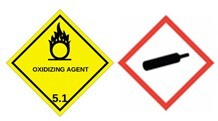
Oxidizing gas
(e.g. Oxygen, Carbogen, Nitrous oxide)
Oxidizing gases should firsthand be stored in the gas storage room in the block and brought out to the laboratory premises temporarily when needed.
Note that oxidizing gases should not be stored together with flammable gases.

Corrosive gas
(e.g. Sulphur dioxide, Chlorine, Hydrogen chloride.)
Corrosive gases chemically attack and damage skin, eyes and mucous membranes on contact. Corrosive gases can affect people to varying degrees, ranging from mild and irritating injury, to severe corrosive damage, depending on concentration and situation.
4. Radiation protection
All work-related activities with radioactive substances or technical devices capable of generating ionising radiation must be carried out in accordance with the Swedish Radiation Protection Act (1988:220), the Radiation Protection Ordinance (1988:293), Regulations from the Swedish Radiation Protection Authority and local radiation protection rules.
Before work/research involving radiation is initiated some requirements must be fulfilled.
Isotope facilities at Biomedicum.
Radiation safety at Karolinska Institutet.
Strålsäkerhetsmyndigheten / Swedish Radiation Safety Authority.
Biomedicum's Radiation safety representative
Ingrid Delin
Coordinator5. Personal Protective Equipment (PPE)
Read more on protective measures when working with chemicals and biosafety at KI central webpages. Always make a written risk assessment before work to minimize the risk of exposure. Use a ventilated workplace when required.
Lab coats
Lab coats should be worn in the laboratories but removed when leaving the lab and when entering common and office areas.
- Clean lab coats can be picked up from the room for clean lab glass ware on each floor. If you need clean and autoclaved lab coats, send a ticket to FM Helpdesk to order autoclaved lab coats.
- Change lab coats frequently. Dirty lab coats should be placed in the quarter recycle room. Please empty pockets before returning the lab coat.
- If you have a contaminated lab coat that needs to be autoclaved (decontaminated) prior to being washed, place it in an autoclave bag and place it in the quarter recycling room. Heavily contaminated lab coats should be disposed of in the yellow laboratory waste bins.
Googles
Use protective googles when working with corrosive chemicals or when needed according to the risk assessment.
Gloves
Protective gloves should be removed before you leave the lab. Protective gloves should be selected based on the application. At Biomedicum Supply center a variety of gloves can be purchased.
6. Internal transport of biological specimens and chemical products
Transportation of biological specimens and chemical products must always be performed in a safe way for both people and the environment.
This information applies to indoor transport through public areas (elevators, culvert, open entrance floor etc.) in Biomedicum and on walkways within the campus area.
Transport guidelines for Biomedicum have been established based on KI instructions .
- A written risk assessment must be performed by the research group for each type of transport, and the group leader is responsible to ensure that employees follow the routines.
- The amount of biological material and chemical products being transported should be minimized, and busy hours, e.g. lunch time, should be avoided for transport.
- The material must be packed so that leakage / spillage is prevented at all times. For guidance, see the KI document "How to Pack Specimens Correctly". Shopping baskets or other transport packaging must be used.
- Personal protective equipment (PPE) is not allowed in public areas and should not be needed during transport.
- If access to Biomedicum transport elevators or liquid nitrogen elevators is needed, contact FM Helpdesk. NB never take the elevator together with liquid nitrogen. Use the stairway or use the service from FM for transport.
- Dry ice can be transported in the elevators. Use a lid for the container.
- Transport of large quantities (ie several work samples or a few bottles) of biological / chemical materials can only be via the personnel elevators if the risk assessment shows it is without risk.
- Transports of biological specimen or chemical products between Biomedicum and BioClinicum should be via culvert on floor 2 and never via the airway on floor 4.
- Major transports, or relocation of chemical storages (which include more than a few work samples of a few bottles), must always be carried out by a moving company.
- Incidents related to transport of biological / chemical material in Biomedicum must be reported in KI's incident reporting system. Incidents related to Bioclinicum should be reported in both incident reporting systems.